Description
EPOXITE FLOOR PAINT 2K is a high performance 2 component solvent based epoxy paint with a gloss finish. It is used to protect and decorate interior floors, walls and many structural surfaces. It is also used to protect polyester or metal structures. It has excellent adhesion, high coverage, high hardness and great resistance to friction and mechanical stress. It is resistant to chemicals and permanent contact with water. Its special formulation, silane fortified with UV filters ensures a durable finish with a long service life.
ADVANTAGES
- Excellent adhesion and hardness
- High coverage
- High resistance to friction and mechanical stress
- High chemical resistance
- High resistance to permanent contact with water
- Silane fortified – Excellent adhesion
- Ensures a durable finish
- Contains UV filters
- Gloss finish – easy to clean
APPLICATIONS
- Suitable for painting concrete floors in factories, warehouses, garages, workshops. Also suitable for painting metal structures and in general surfaces that are subjected to frequent stress from friction and chemicals.
- Suitable for application on concrete, screeds, stone, metallic, wooden and GRP surfaces when treated accordingly.
- Suitable for indoor use.
Specifications
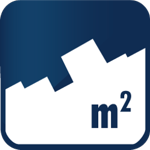 |
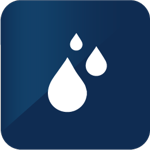 |
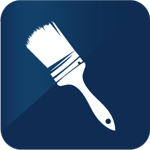 |
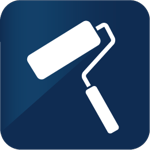 |
Coverage:
300 – 450 gr/m2 for 2or 3 layers
|
Thinning:
0 – 5% with DIL X 100 Solvent
|
Application:
by brush
|
Application:
by roller
|
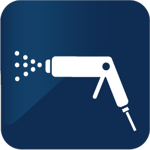 |
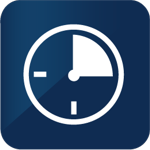 |
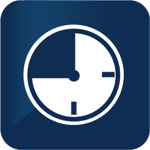 |
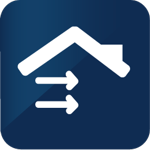 |
Application:
by spray gun
|
Touch dry:
2 hours
|
Hard dry:
7 days
|
Interior use
|
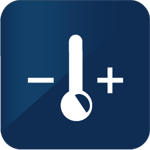 |
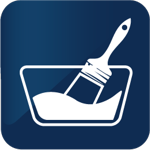 |
|
|
Application temperature:
+10oC to +35oC
|
Cleaning:
with DIL X 100 solvent
|
|
|
Instructions for use
Surface preparation
- Surfaces should be dry and clean from dust and any oily residues. Dust, oil, humidity or rust seriously affect the coating’s adhesion.
- Loose substrates of concrete and screeds are not suitable for painting as the coat will peel. The cementitious substrate needs to be mechanically prepared (e.g., by sanding, shot blasting, or milling) to smooth out any irregularities, open the pores, and ensure better adhesion. Strengthen substrates with the special solvent-free primer EPOXITE DRYMAX WET 2K or EPOXITE DUR 2K in one or two layers depending on the substrate’s porosity. Cementitious surfaces must be made of concrete grade C20/25 and above, and cement mortars must have a cement content of at least 350kg/m2 with at least 1.5Mpa tensile strength.
- New surfaces of concrete or cement mortar should be painted one month after construction. Substrates moisture should not exceed 4%.
- If the surface gets wet, allow it to dry for at least 2 – 5 days prior to the paint application (<4% Substrate’s moisture).
- Repairs and surface smoothing can be done using appropriate products, such as the epoxy putty EPOXITE CONSTRUCT, or a mixture of EPOXITE DRYMAX WET with M-32 quartz sand (suggested mixing ratio 1:1-2), after proper priming.
Priming
Prime cementitious surfaces with EPOXITE DUR 2K solvent based primer. Surfaces with rising humidity should be primed with 100% solids 2 component epoxy primer EPOXITE DRY MAX WET. On stable substrates, the paint can also be used as a primer diluted 10% with DIL X 100 solvent. A second coat of primer may be required to fully seal the substrates porosity.
Metal surfaces are primed with the special anti-osmosis & anticorrosive epoxy primer ALL in ONE EPOXY PRIMER P-76.
Previous paints in good condition should be sanded first. Remove dust using a professional vacuum cleaner and proceed as for cementitious surfaces.
Previous paints in poor condition must be completely removed by mechanical means. Remove dust using a professional vacuum cleaner and proceed as for cementitious surfaces.
Application of the paint follows after the primer has dried: 12 to 24 hours. If 24 hours have passed, the primer must be lightly sanded for better adhesion of the paint.
Application
- Components Α (resin) and Β (hardener) are already packed in separate containers with a preset mixing ratio. Any modification of the mixing ratio will result in improper polymerization of the mixture.
- Mix the 2 components after carefully mixing each component separately.
- Stirring is done carefully for 3-5 minutes taking care to ensure thorough mixing of the two components on the walls and the bottom of the pail.
- Imperfect mixing will result in uneven curing of the coating with parts that will not cure at all.
- After mixing the two components, allow 5 minutes and then apply the 1st coat diluted 0% to 5% with DIL X 100 solvent.
- 24 hours later, apply the second coat diluted 0% - 5% with DIL X 100 solvent.
- Application is done with a brush, roller, or spray gun in two coats. A third coat is recommended for commercial use.
- The paint obtains its final properties 7 days after the application of the finishing coat (at 25oC).
- Mix only as much material as can be applied within the pot life.
REMARKS
- Application conditions: Substrate’s moisture: <4%, Surface’s and Ambient temperature: 12oC - 35oC, Relative Air Humidity: <70%.
- Freshly painted surfaces must be protected from excessive humidity and rain for 36 – 48 hours.
- EPOXITE FLOOR PAINT 2K contains solvents, and during application, good ventilation of the space should be ensured.
- It is advisable to use protective clothing, gloves, hat, and mask with a filter suitable for solvents.
- If recoating is carried out after 48 hours, the surface must be sanded with coarse sandpaper and dust must be removed.
- Curing, as well as pot life, are affected by ambient temperature and humidity. Low temperatures and high humidity tend to increase pot life, while high temperatures and low humidity shorten the pot life.
- Before using EPOXITE FLOOR PAINT 2K, carefully read all instructions and information relevant to its safe and best use (Safety Data Sheet).
- After fully cured, EPOXITE FLOOR PAINT 2K is totally safe for health.
CLEANING
Clean tools with DIL X 100 solvent.