Description
PU FLEX 1000 is one component liquid-applied, permanently highly elastic, 100% polyurethane membrane used for long-lasting waterproofing. Due to the polyurethane technology, it offers the solution to sealing problems where other methods fail, such as on surfaces with ponding water and ice. Cures by reaction with atmospheric moisture and forms a highly water repellent and 100% waterproof membrane.
ADVANTAGES
- Lifetime expectancy up to 25 years
- Simple application (1 component – ready to use)
- Forms a walkable uniform seamless membrane
- Resistant to water
- Resistant to frost
- Maintains its mechanical properties over a temperature range of -40oC to +90oC
- Crack-bridging up to 2mm (max. -10oC)
- Water vapour permeability
- Excellent adhesion to the substrate
- Excellent UV resistance
- Defects can be easily repaired locally within minutes
- Highly cost effective
APPLICATIONS
- Waterproofing of roofs, balconies and terraces
- Waterproofing of wet areas (under-tile) in bathrooms, balconies, kitchens, etc.
- Protection of polyurethane foam insulation and alternative insulation panels
- Waterproofing of flowerbeds and foundations
- Waterproofing and protection of concrete constructions like bridge-decks, tunnels, etc.
Specifications
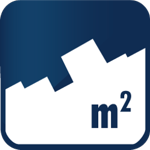 |
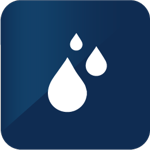 |
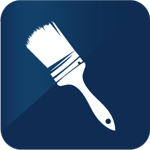 |
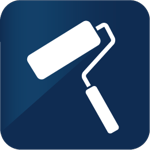 |
Coverage:
1,2 - 1,8 kg/m2 applied in two or tgree layers
|
Thinning:
0% to 10% with DIL X 100 solvent
|
Application:
by brush
|
Application:
by roller
|
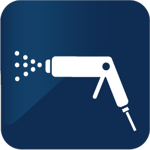 |
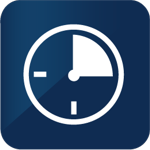 |
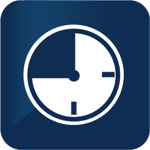 |
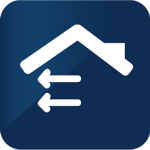 |
Application:
by spray gun
|
Touch dry:
3 - 4 hours
|
Hard dry:
7 days
|
Exterior use
|
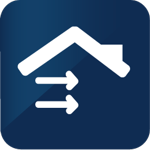 |
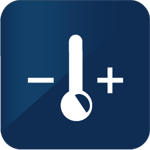 |
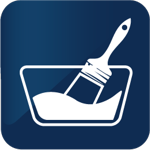 |
|
|
Interior use
|
Application temperature:
+5oC - 38oC
|
Cleaning:
With DIL X 100 solvent
|
|
|
Instructions for use
Substrate preparation
Careful surface preparation is very important for optimum finish and durability.
- The surface needs to be clean, dry, sound, and free of any contamination that may harmfully affect the adhesion of the membrane.
- Maximum substrate moisture content should not exceed 5%.
- New concrete structures need to dry for at least 28 days.
- Old, loose coatings, dirt, fats, oils, organic substances, and dust need to be removed by mechanical means such as a sanding machine. Possible surface irregularities need to be smoothened.
- Clean substrate thoroughly before application.
Repair of cracks
The careful sealing of existing cracks and joints before the application is extremely important for long lasting waterproofing results.
- Clean cracks and hairline cracks from dust, residues, or other contamination.
- Small cracks up to 2 – 3mm must be primed locally with solvent-based primer PU 900 and allowed to dry. Apply locally one coat of PU FLEX 1000, and on the wet coat dip a fibre net (30gr/m2) or fibre tape (60gr/m2) 4 - 10cm wide, then recoat with PU FLEX 1000.
- Larger cracks and expansion joints must be primed locally with polyurethane primer PU 900 and filled with polyurethane sealant BONDFLEX 290 LM.
Priming
- Prime absorbent surfaces like concrete, cement screed, and wood with solvent-based primer PU 900. Allow drying for 2 – 4 hours.
- Prime non-porous or difficult surfaces (metal, ceramic tiles, plastics) with epoxy-based primer EPOXITE DUR AQUA.
Application
- Stir well before use and dilute PU FLEX 1000 up to 10% with DIL X 100 solvent.
- Pour the PU FLEX 1000 onto the primed surface and spread it using a roller or brush until the entire surface is covered. You can use an airless spray, allowing for considerable manpower savings.
- After 12 hours (not later than 36 hours), apply another layer of the PU FLEX 1000 crosswise. If necessary, apply a third layer of PU FLEX 1000. For larger areas, airless spray application is recommended to save time.
RECOMMENDATION
Reinforcement of the entire surface with fibre mesh 60 – 90gr/m2 is recommended. Use 5-10cm stripe overlapping. Always reinforce with the fibre cloth at problem areas, like wall-floor connections, chimneys, pipes, waterspouts (siphon), etc. To do this, apply a correctly cut piece of non-woven fibre cloth on the still wet PU FLEX 1000, press it to soak, and saturate again with enough PU FLEX 1000.
ATTENTION
Do not apply PU FLEX 1000 over 0.6 mm thickness per layer (0.9kg/m2). For best results, the temperature during application and curing should be between 5oC and 35oC. Low temperatures delay curing, while high temperatures speed up curing. High humidity may affect the final finish.